
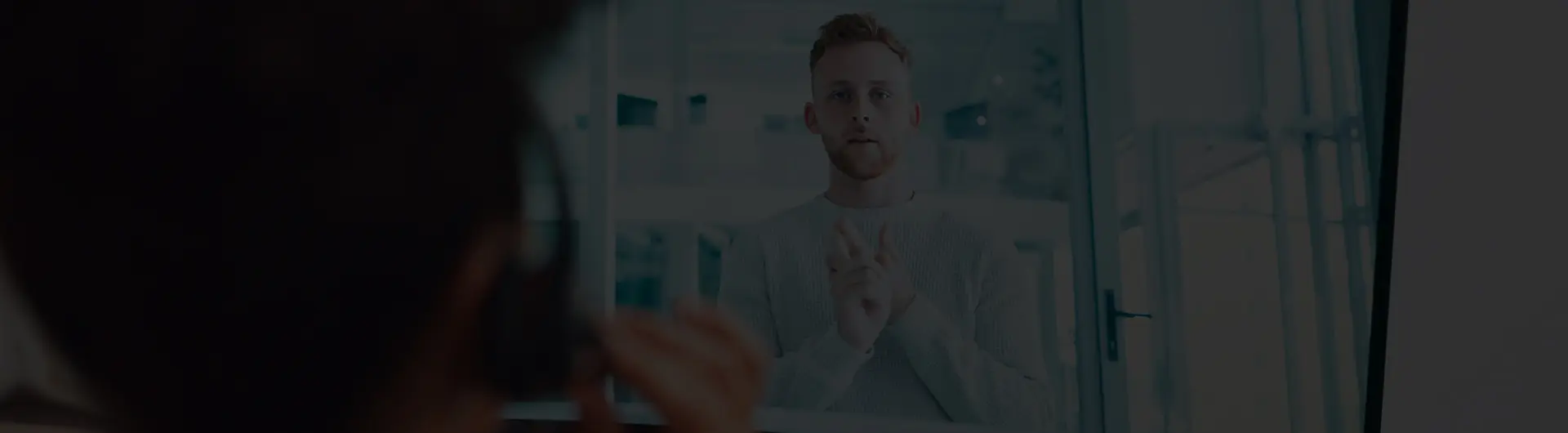
Unlocking Precision: Essential Tips for Choosing the Right Ring Load Cell for Your Needs
In the world of industrial weighing and force measurement, the selection of the appropriate Ring Load Cell is crucial for optimizing accuracy and performance. According to a recent report by the Global Weighing Industry Association, the demand for load cells is projected to reach $1.2 billion by 2025, with ring load cells accounting for a significant portion of this growth. This increasing reliance on precise measurement solutions across various applications, including automotive, aerospace, and manufacturing, underscores the importance of understanding the nuances involved in choosing the right load cell for specific tasks.
Choosing the right Ring Load Cell is more than just a technical specification; it can impact operational efficiency, safety, and overall performance. A study published in the Journal of Advanced Materials highlights that improper selection can lead to measurement errors of up to 10%, resulting in substantial financial losses and operational delays. As industries continue to prioritize precision and reliability, it becomes essential for engineers and decision-makers to gain insights into the selection process, ensuring their load cell solutions align perfectly with their operational needs and industry standards.
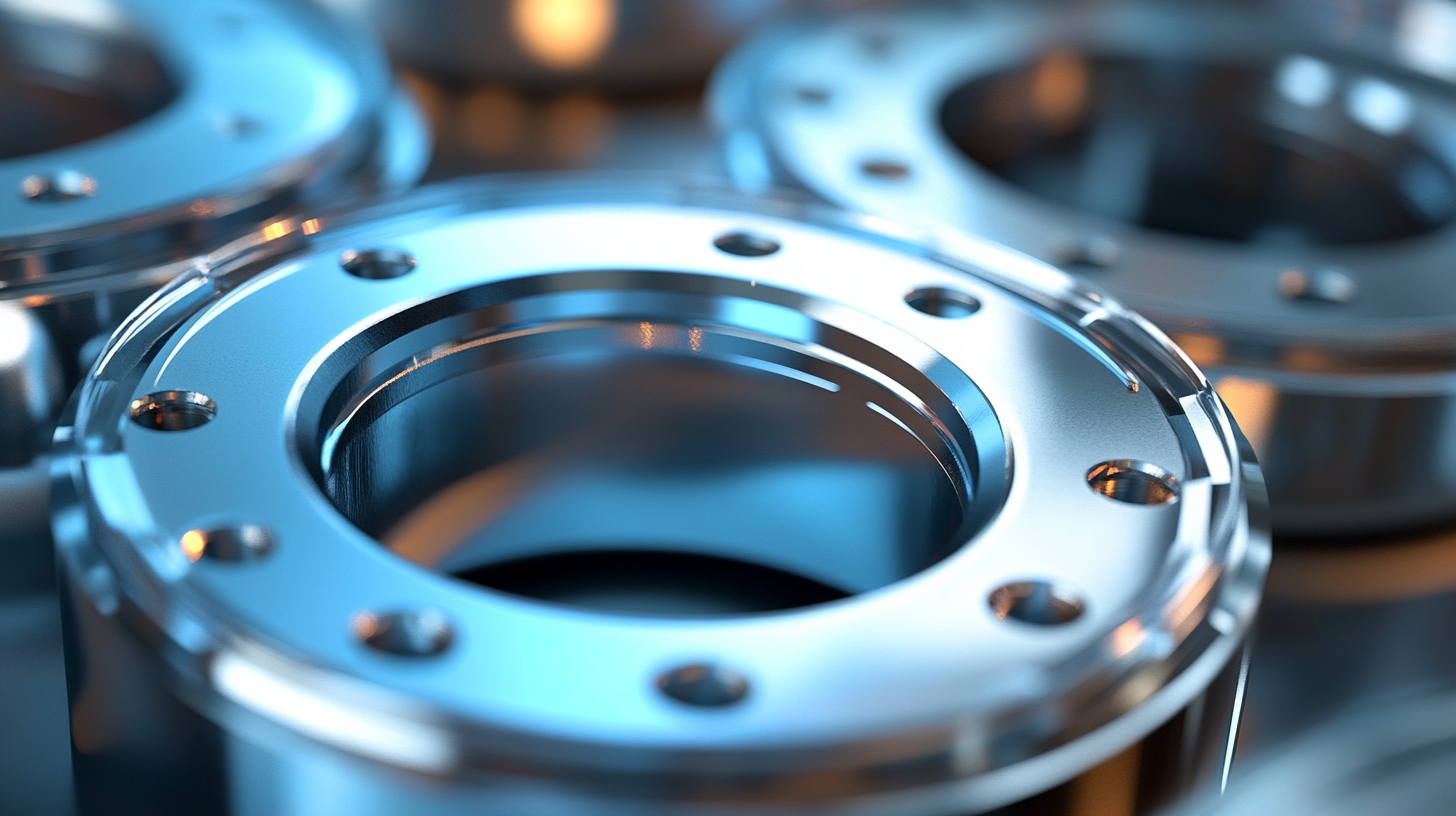
Understanding the Basics: What is a Ring Load Cell and How Does It Work?
A ring load cell is a specialized type of load cell designed to measure force or weight in a variety of applications. Its unique ring shape allows it to accommodate limited space while also providing high accuracy in measurements. This design is particularly beneficial in situations where forces are applied from multiple directions, making ring load cells a preferred choice in industries such as automotive, aerospace, and manufacturing. Understanding how a ring load cell works involves grasping the principle of strain gauges. These gauges are strategically placed on the cell and detect changes in resistance as the load is applied. When force is exerted on the ring, it deforms slightly, and the strain gauges convert this deformation into an electrical signal that can be measured and calibrated. This process ensures that even small changes in weight can be accurately captured, providing precise data for engineers and operators. Ring load cells also come with varying capacities and sensitivities, catering to specific applications. When choosing a ring load cell, it's essential to consider factors such as load capacity, material compatibility, and environmental conditions, as these elements can significantly affect performance. By understanding these basic principles, users can ensure they select the right ring load cell to meet their precise measurement needs.
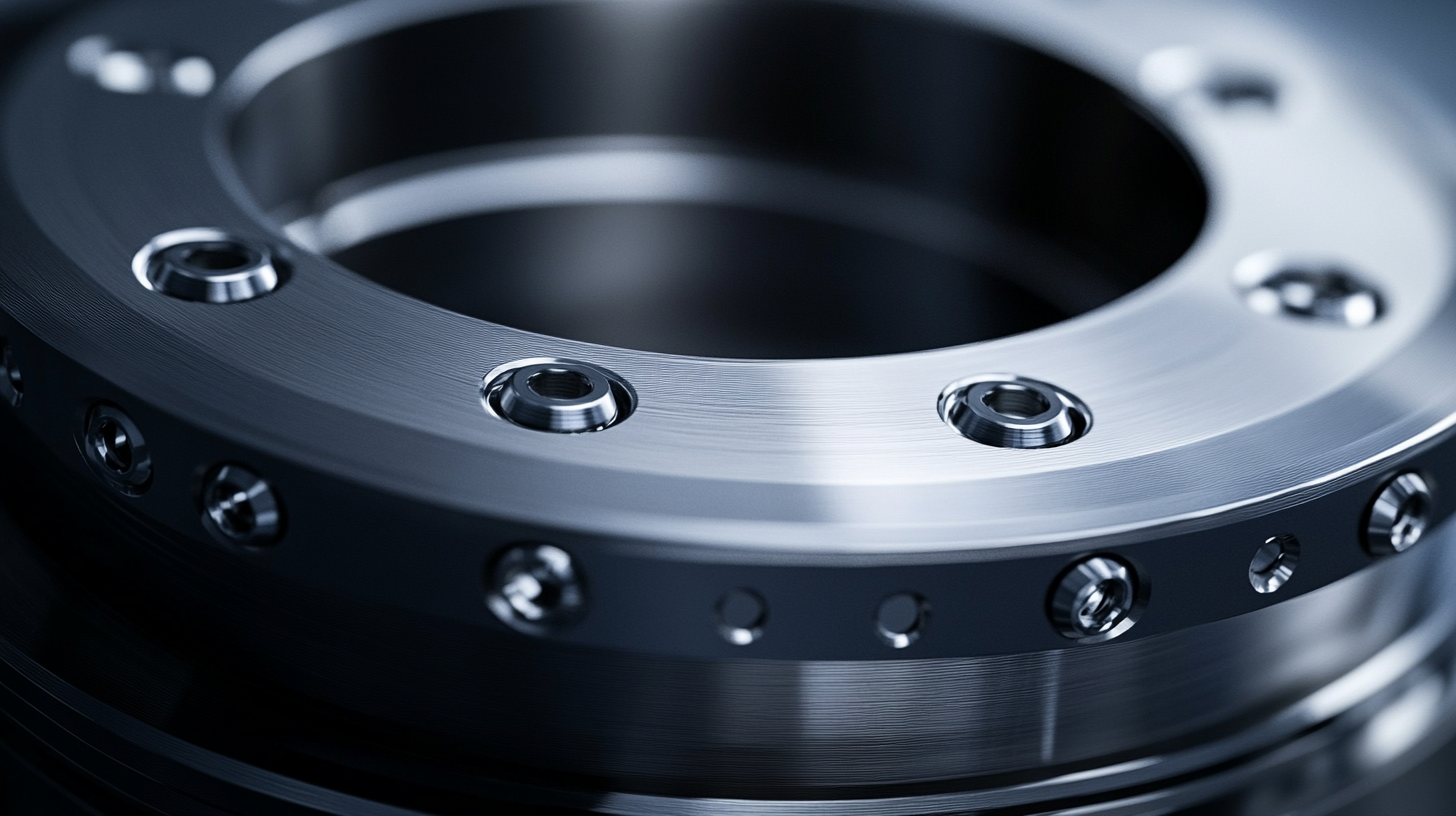
Key Factors to Consider: Load Capacity and Measurement Range
When selecting a ring load cell, two critical factors to consider are load capacity and measurement range. Load capacity refers to the maximum weight that the load cell can accurately measure. It’s essential to choose a load cell with a capacity that exceeds your expected loads to prevent damage and ensure reliable readings. Overloading a load cell can lead to permanent deformation, affecting accuracy and safety. Therefore, evaluating your application’s weight requirements is vital in determining the appropriate load capacity for your ring load cell.
Measurement range complements load capacity by defining the scope within which the load cell can operate effectively. A ring load cell should ideally encompass the anticipated range of forces or weights during its usage. Selecting a load cell with a too narrow measurement range may result in inaccurate readings or limitations in your application. Conversely, an overly broad range may introduce additional uncertainty or variability in measurements, which can hinder precision. It’s crucial to analyze the specific dynamics of your application to ensure the load cell’s measurement range aligns with your operational needs, thus achieving optimal performance and accuracy.
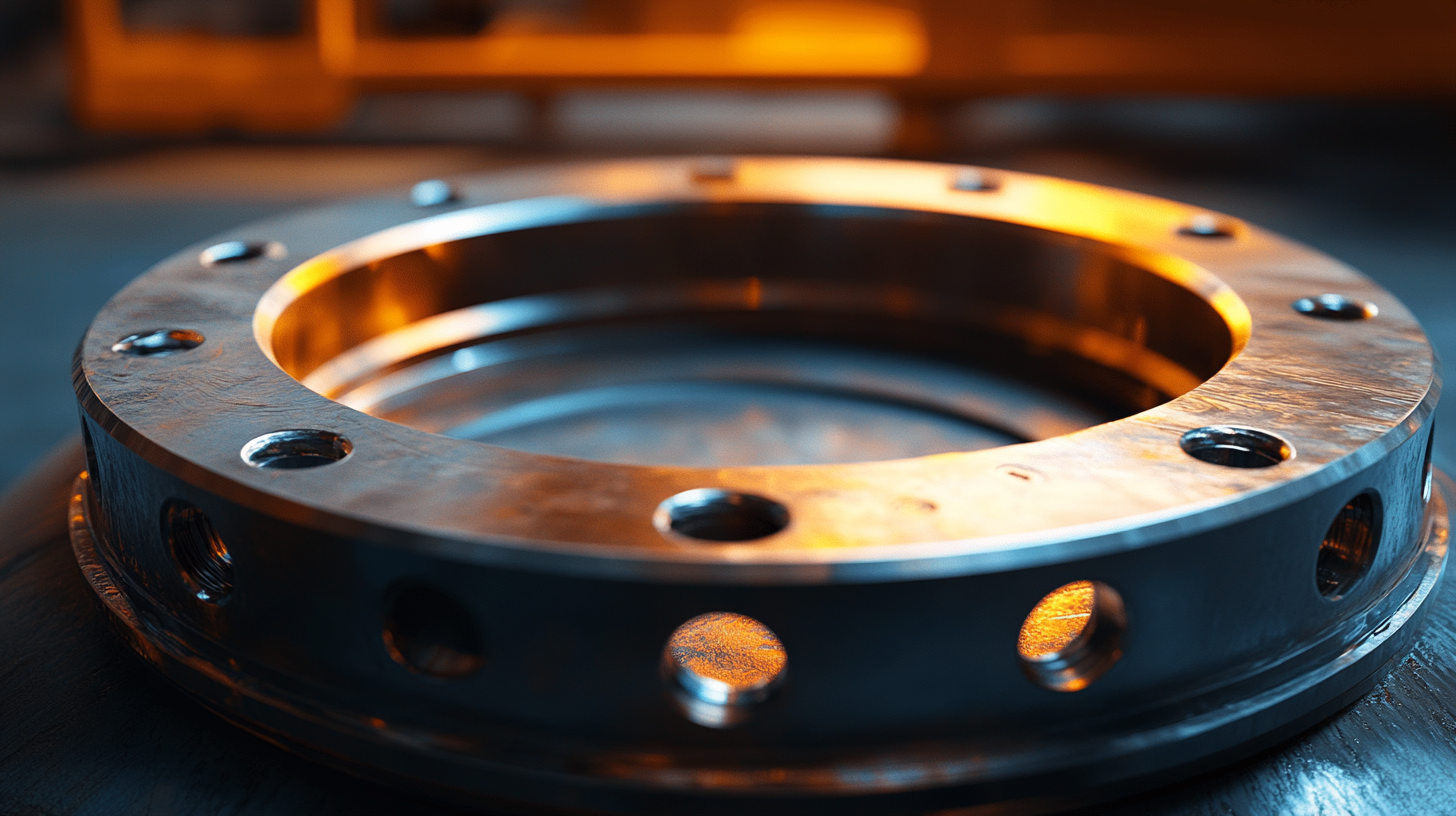
Material Matters: Choosing the Right Construction for Longevity
When it comes to selecting a ring load cell, the material of construction plays a pivotal role in determining its durability and performance. Different applications may expose load cells to harsh environmental conditions, such as extreme temperatures, humidity, or corrosive substances. Therefore, opting for materials specifically engineered for resilience is essential. Common materials include stainless steel, aluminum, and specialized alloys, each offering unique benefits. Stainless steel, for instance, is highly resistant to corrosion, making it ideal for applications in chemical industries or outdoor environments.
Furthermore, the manufacturing process and surface treatments can significantly impact the longevity of a load cell. For instance, load cells that undergo anodizing or coating treatments enhance their resistance to wear and tear, effectively prolonging their lifespan. Understanding the specific environmental factors and load requirements of your application can guide you in selecting the most appropriate material. Certain applications might even benefit from custom materials designed to withstand specific circumstances, providing an extra layer of reliability for critical measurements.
In conclusion, prioritizing the right construction material when choosing a ring load cell is not merely about aesthetics; it is a crucial decision that affects overall performance and lifespan. By investing time in understanding the available materials and their properties, you can ensure that your load cell will function optimally, even in the most demanding conditions.
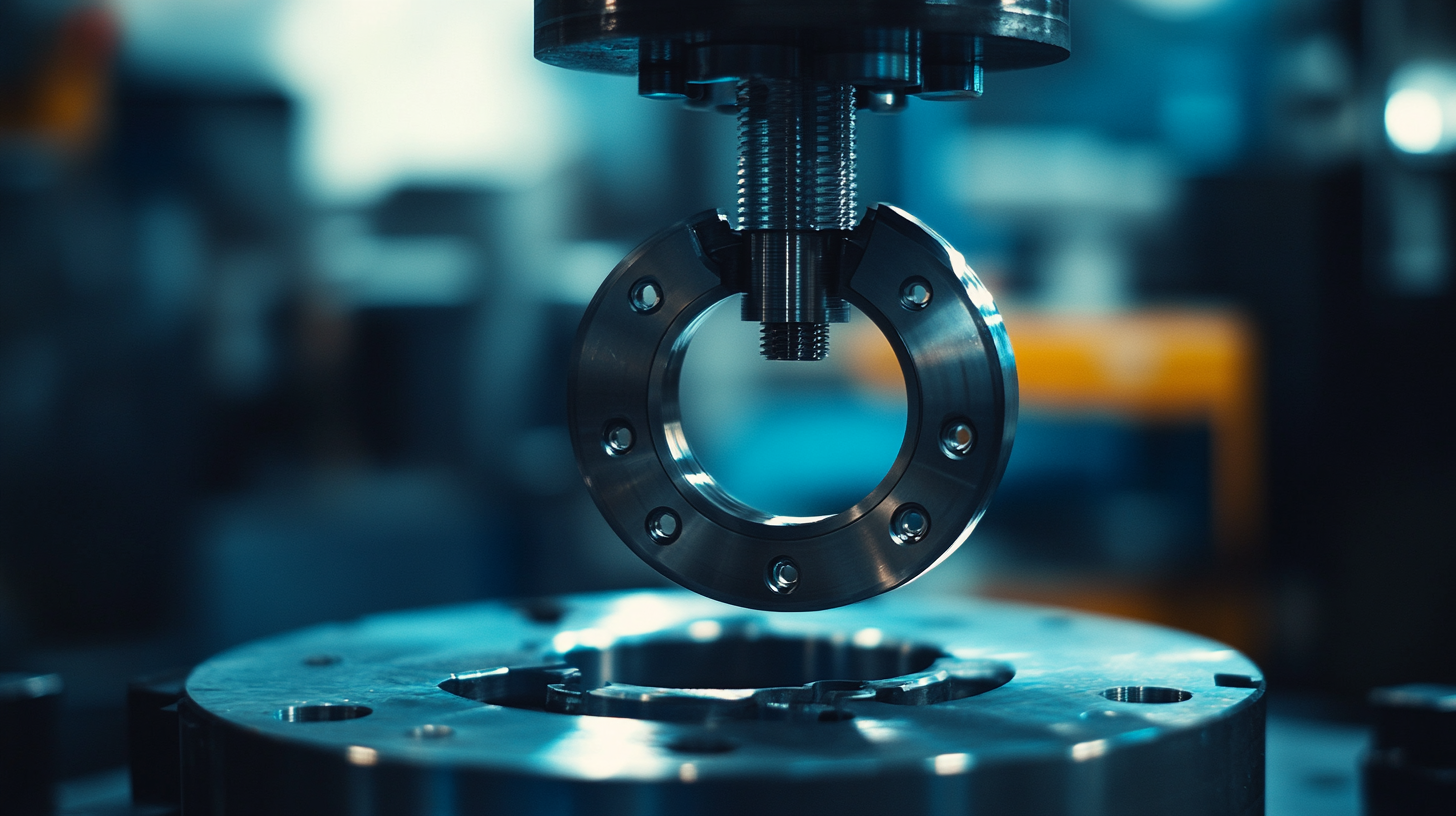
Accuracy vs. Sensitivity: Finding the Balance for Your Application
When selecting a ring load cell, understanding the balance between accuracy and sensitivity is paramount for achieving optimal performance in various applications. Accuracy refers to how closely a load cell's measurements align with the actual load, while sensitivity indicates the load cell's ability to detect small changes in load, often expressed in microstrain or millivolts per volt (mV/V). According to a report by the International Society of Automation, high-accuracy load cells typically achieve an accuracy class of better than 0.05% of full scale, but achieving such precision often comes at the expense of sensitivity, particularly in challenging environments.
In many industrial applications, the choice of load cell hinges on the specific demands of the task at hand. For example, in precision weighing tasks in the pharmaceuticals industry, load cells with a high accuracy rating are required to ensure product safety and compliance with stringent regulations. Conversely, in applications like structural monitoring, where minute changes in load must be detected, sensitivity takes precedence. The National Institute of Standards and Technology emphasizes that using a load cell with greater sensitivity can be critical in processes where even slight deviations significantly impact overall outcomes.
Furthermore, the data from the Load Cell Manufacturers Association indicates that advancements in materials and technology are helping to bridge the gap between accuracy and sensitivity. Innovative designs utilizing advanced materials can improve both characteristics, allowing for more versatile applications. Therefore, selecting the right ring load cell requires a careful assessment of your specific operational needs, weighing the trade-offs between accuracy and sensitivity to ensure your application achieves its objectives effectively.
Installation Considerations: Tips for Proper Setup and Calibration
When it comes to achieving optimal picture quality for your television setup, proper calibration is key. Many consumers overlook this step and opt for factory settings that often fail to deliver the best viewing experience. Studies indicate that professionally calibrated TVs can provide color accuracy improved by over 30% compared to their default settings. However, you can achieve substantial improvements without spending money on calibration services or discs.
To start, familiarize yourself with your TV’s picture settings. Most modern televisions have presets for different environments—choose one close to your typical viewing conditions. For instance, a “movie” mode generally offers better color accuracy than “vivid” mode, which can oversaturate colors. Adjust brightness and contrast according to your room lighting; a good rule of thumb is to set brightness to just below the maximum level that causes white clipping, ensuring that bright scenes remain detailed.
Once you have established these basic settings, dive deeper into fine-tuning. Use online tools or test patterns available through streaming services. Setting gamma to the right level (around 2.2 for most displays) can also enhance shadow detail and overall fidelity. Simple adjustments such as reducing sharpness may improve the natural look of images while calibrating color settings to match real-world tones can further enhance the viewing experience.
Lastly, keeping your TV's firmware updated ensures that you have access to the latest features and fixes that manufacturers implement for performance improvements. Regularly revisiting your calibration settings is also crucial, especially after firmware updates, to ensure that picture quality remains at its peak. Investing some time into this process can transform your viewing experience, resulting in a much more enjoyable engagement with your favorite content.